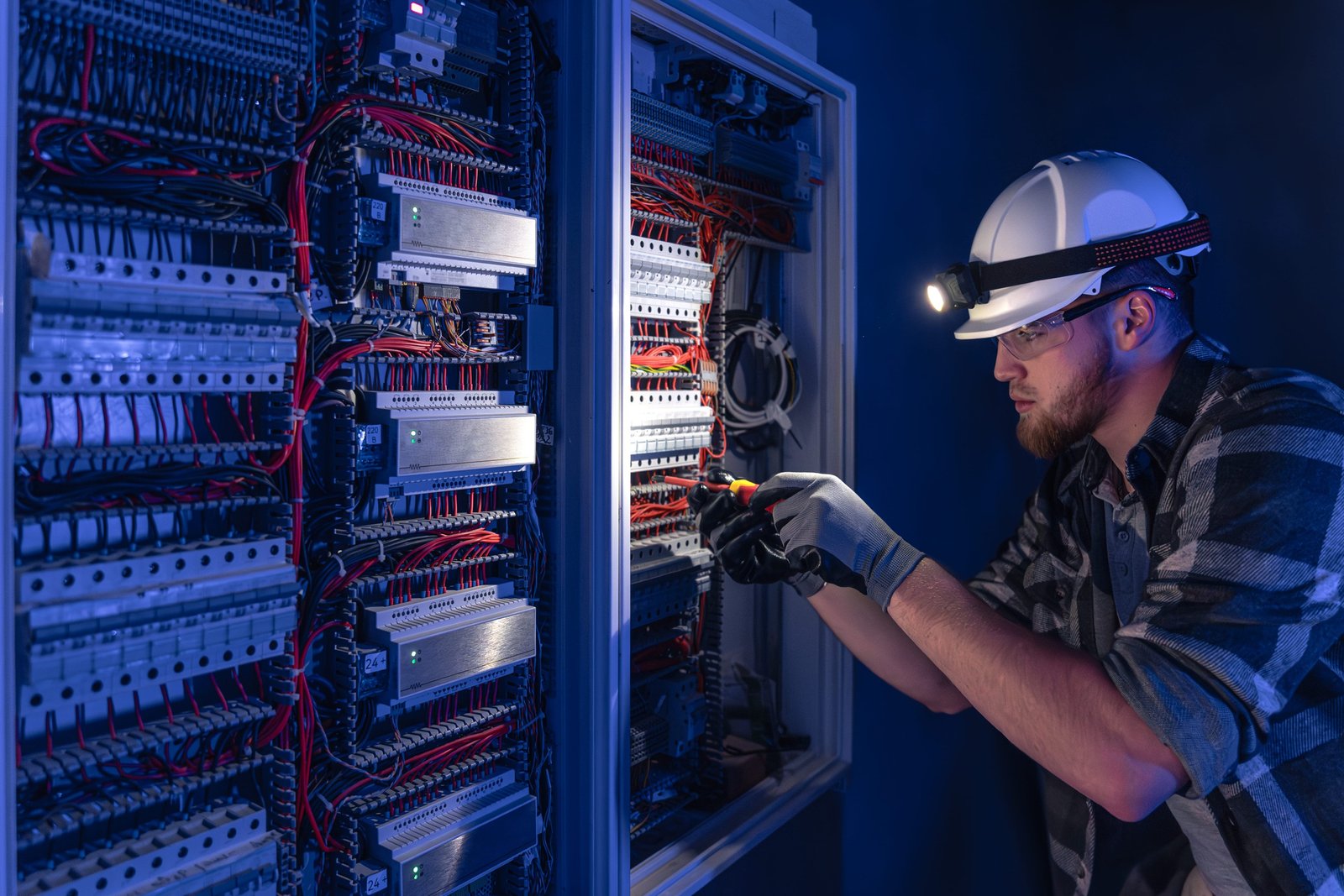
Electric Motor Protection and Control Systems: An In-depth Overview
Electric motor protection and control systems are vital components in the operation and safeguarding of electric motors. These systems ensure that electric motors run efficiently, safely, and reliably in various industrial and commercial applications. In this article, we will explore the key components, functions, applications, product architecture, and advantages of electric motor protection and control systems, highlighting the significant role these systems play in motor protection.
Components of Electric Motor Protection and Control Systems
Electric motor protection and control systems are typically composed of several essential components, each serving a specific role to ensure the motor’s efficient operation:
- Motor Protection Relays: These relays are designed to protect the motor from abnormal operating conditions such as overcurrent, undercurrent, short circuits, and phase failure. They also detect and react to issues like thermal overload and insulation failure, preventing motor damage.
- Circuit Breakers: A circuit breaker is a safety device that automatically disconnects the electrical supply in case of overloads or short circuits. It protects the motor from electrical damage by ensuring the circuit is quickly interrupted if a fault occurs.
- Overload Protection Devices: These devices monitor the motor’s current and temperature to prevent overheating. Overload protection is crucial for preventing motor burnouts caused by excessive current draw or improper cooling.
Variador de frecuencia de alto rendimiento serie CF40-B
- Motor Starters: Motor starters are essential for controlling the motor’s start-up and shutdown processes. They help regulate the inrush current during motor startup and provide protection against electrical faults.
Arrancador suave de estado sólido para motor de alta tensión serie HVLTICM
- Control Panels: The control panel integrates all components of the motor protection and control system. It houses the relays, circuit breakers, starters, and other monitoring devices, providing a centralized location for managing the motor’s protection and control.
Functions of Electric Motor Protection and Control Systems
The primary functions of electric motor protection and control systems are designed to ensure the safety, reliability, and longevity of the motor. Key functions include:
- Overload Protection: Prevents the motor from drawing excessive current, which could lead to overheating and potential motor failure.
- Phase Failure and Unbalance Protection: Detects any phase loss or unbalance, which could damage the motor or reduce its efficiency.
- Short Circuit Protection: Immediately interrupts the power supply to the motor in case of a short circuit, preventing severe damage to the motor and the surrounding electrical infrastructure.
- Thermal Protection: Monitors the motor’s operating temperature and provides protection if the temperature exceeds safe limits.
- Earth Fault Protection: Ensures that the motor’s electrical system is safely grounded to prevent electric shocks or fire hazards.
Applications of Motor Protection and Control Systems
Electric motor protection and control systems find applications in numerous industries, where the continuous and safe operation of motors is critical. Some common application areas include:
- Industrial Manufacturing: Electric motors drive machines such as conveyors, pumps, fans, and compressors in factories. These motors require constant protection to avoid unexpected failures that can halt production lines.
- HVAC Systems: Motors used in heating, ventilation, and air conditioning systems are vital to maintaining comfort and air quality. Protection systems ensure they remain operational and avoid overheating or damage during intense use.
- Water and Wastewater Treatment Plants: Pumps and motors in water treatment facilities are essential for the movement and processing of water. These motors must be protected from issues like overcurrent, phase failure, and thermal overload to ensure uninterrupted operation.
- Mining and Oil & Gas: In the mining industry and oil extraction operations, electric motors are used in heavy-duty equipment such as drills, pumps, and compressors. These environments often involve high levels of risk, making motor protection systems essential for worker safety and equipment longevity.
- Renewable Energy: Wind turbines and solar inverters rely on electric motors for operation. Effective protection and control systems ensure these motors operate optimally in varying environmental conditions.
Product Architecture of Electric Motor Protection and Control Systems
The architecture of an electric motor protection and control system can vary based on the complexity of the motor’s application. Generally, a well-designed system includes:
- Protection Relays: Devices that monitor motor performance, providing real-time data on conditions such as overcurrent, temperature, and voltage imbalances.
- Control Panels: These panels are equipped with all necessary components, such as circuit breakers, overload relays, and motor starters, for motor protection and control.
- Sensors: Various sensors are integrated into the system to monitor temperature, voltage, current, and other operational parameters of the motor.
- Communication Interfaces: Many modern systems include communication modules that allow remote monitoring and control. This is particularly useful in large-scale industrial applications, where real-time diagnostics and alerts are critical.
Advantages of Linvent Electric Motor Protection and Control Products
When it comes to choosing a reliable provider for motor protection and control systems, Linvent Eléctrico stands out as a trusted brand known for its high-quality products. Here are some advantages of Linven’s electric motor protection and control solutions:
- Comprehensive Protection Features: Linvent offers a wide range of motor protection relays and control systems that protect against overloads, short circuits, phase failure, and more, ensuring the motor operates under optimal conditions at all times.
- High-Quality Components: Linvent products are designed with durable components to withstand harsh industrial environments, ensuring longevity and reduced downtime.
- Ease of Use and Installation: Linvent’s user-friendly interfaces and simple installation processes make it easy for businesses to integrate protection systems into their operations without significant downtime or training.
- Customizable Solutions: Linvent offers tailored motor protection solutions to meet the unique needs of various industries, ensuring maximum efficiency and safety for every application.
- Remote Monitoring and Control: With advanced communication features, Linvent’s motor protection systems enable remote monitoring, providing businesses with the ability to track motor health and receive real-time alerts on potential issues.
Conclusión
Electric motor protection and control systems are critical to ensuring the safety, efficiency, and longevity of electric motors in various industrial applications. With components like motor protection relays, circuit breakers, and control panels, these systems offer comprehensive protection against overloads, short circuits, and other electrical faults. For businesses looking to secure their motors and reduce the risk of downtime, Linvent Eléctrico provides top-tier motor protection and control products designed to meet the highest standards of performance, durability, and ease of use.
By investing in Linven’s motor protection systems, businesses can ensure that their electric motors remain in optimal condition, thereby minimizing downtime and maximizing productivity.
Perfil del autor
Últimas entradas
IoT2025-04-14Electrical Automation – The Indispensable Behind-the-Scenes Hero of the Internet of Things
Conocimientos de automatización eléctrica2025-04-11Electrical Automation Solutions in the Energy Storage Industry: Applications, Advancements, and Benefits
Seguridad y protección eléctrica2025-04-06Electric Motor Protection and Control Systems: An In-depth Overview
Conocimientos de automatización eléctrica2025-04-01The Application of Electrical Automation in the New Energy Industry